Порьозност, прекъсвания от тип кухина, образувани от улавяне на газ по време на втвърдяване, е често срещан, но тромав дефект при MIG заваряване и има няколко причини. Може да се появи в полуавтоматични или роботизирани приложения и изисква премахване и преработване и в двата случая - което води до прекъсване и увеличаване на разходите.
Основната причина за порьозност при заваряване на стомана е азотът (N2), който се включва в заваръчната вана. Когато течният басейн се охлади, разтворимостта на N2 е значително намалена и N2 излиза от разтопената стомана, образувайки мехурчета (пори). При поцинковано/поцинковано заваряване, изпареният цинк може да се разбърка в заваръчната вана и ако няма достатъчно време да излезе, преди вана да се втвърди, той образува порьозност. При заваряване на алуминий цялата порьозност се причинява от водород (H2), по същия начин, както N2 действа в стоманата.
Порьозността при заваряване може да се появи отвън или отвътре (често наричана подповърхностна порьозност). Може също така да се развие в една точка на заварката или по цялата дължина, което води до слаби заварки.
Знанието как да идентифицирате някои ключови причини за порьозността и как бързо да ги разрешите може да помогне за подобряване на качеството, производителността и крайния резултат.
Лошо покритие със защитен газ
Лошото покритие със защитен газ е най-честата причина за порьозност при заваряване, тъй като позволява на атмосферните газове (N2 и H2) да замърсят заваръчната вана. Липсата на подходящо покритие може да възникне поради няколко причини, включително, но не само, слаб дебит на защитния газ, течове в газовия канал или твърде силен въздушен поток в заваръчната клетка. Прекалено бързите скорости на пътуване също могат да бъдат виновник.
Ако оператор подозира, че слабият поток причинява проблема, опитайте да регулирате разходомера за газ, за да се уверите, че скоростта е подходяща. Когато използвате режим на прехвърляне на спрей, например, трябва да е достатъчен поток от 35 до 50 кубически фута на час (cfh). Заваряването при по-високи амперажи изисква увеличаване на скоростта на потока, но е важно да не задавате скоростта твърде висока. Това може да доведе до турбуленция в някои конструкции на пистолети, което нарушава покритието на защитен газ.
Важно е да се отбележи, че различно проектираните пистолети имат различни характеристики на газовия поток (вижте два примера по-долу). „Сладкото място“ на скоростта на газовия поток за горния дизайн е много по-голямо от това на долния дизайн. Това е нещо, което инженерът по заваряване трябва да вземе предвид, когато настройва заваръчната клетка.
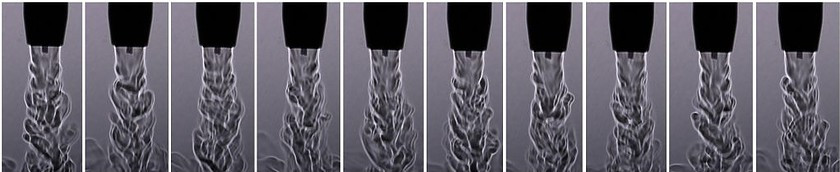
Дизайн 1 показва плавен газов поток на изхода на дюзата
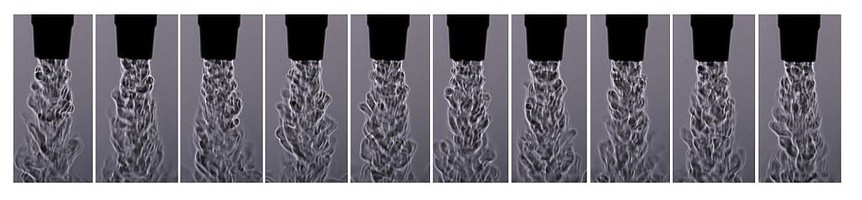
Дизайн 2 показва турбулентен газов поток на изхода на дюзата.
Също така проверете за повреда на газовия маркуч, фитингите и съединителите, както и О-пръстените на захранващия щифт на пистолета за заваряване MIG. Сменете, ако е необходимо.
Когато използвате вентилатори за охлаждане на оператори или части в заваръчна клетка, внимавайте те да не са насочени директно към зоната на заваряване, където биха могли да нарушат покритието на газ. Поставете екран в заваръчната клетка, за да предпазите от външен въздушен поток.
Докоснете отново програмата в роботизирани приложения, за да се уверите, че има подходящо разстояние от върха до работното място, което обикновено е ½ до 3/4 инча, в зависимост от желаната дължина на дъгата.
И накрая, бавни скорости на движение, ако порьозността продължава или се консултирайте с доставчик на MIG пистолет за различни предни компоненти с по-добро покритие на газ
Замърсяване с неблагородни метали
Замърсяването с неблагородни метали е друга причина за появата на порьозност - от масло и грес до котлен камък и ръжда. Влагата също може да насърчи това прекъсване, особено при заваряване на алуминий. Тези видове замърсители обикновено водят до външна порьозност, която е видима за оператора. Поцинкованата стомана е по-податлива на подповърхностна порьозност.
За да се борите с външната порьозност, не забравяйте да почистите добре основния материал преди заваряване и обмислете използването на заваръчна тел с метална сърцевина. Този тип тел има по-високи нива на дезоксиданти от плътната тел, така че е по-толерантен към всички останали замърсители върху основния материал. Винаги съхранявайте тези и всякакви други проводници на сухо, чисто място с подобна или малко по-висока температура от тази на растението. Това ще помогне за минимизиране на конденза, който може да внесе влага в заваръчната вана и да причини порьозност. Не съхранявайте проводниците в хладилни складове или на открито.
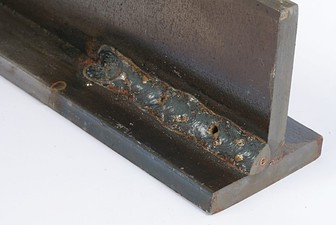
Порьозност, прекъсвания от тип кухина, образувани от улавяне на газ по време на втвърдяване, е често срещан, но тромав дефект при MIG заваряване и има няколко причини.
При заваряване на поцинкована стомана, цинкът се изпарява при по-ниска температура, отколкото се топи стоманата, а бързите скорости на движение водят до бързо замръзване на заваръчната вана. Това може да улови цинкови пари в стоманата, което води до порьозност. Борете се с тази ситуация, като наблюдавате скоростта на пътуване. Отново помислете за специално проектирана (флюсова формула) тел с метална сърцевина, която насърчава излизането на цинкови пари от заваръчната вана.
Запушени и/или маломерни дюзи
Запушени и/или по-малки дюзи също могат да причинят порьозност. Пръски от заваряване могат да се натрупат в дюзата и по повърхността на контактния накрайник и дифузера, което води до ограничаване на потока на защитния газ или го кара да стане турбулентен. И двете ситуации оставят заваръчната вана с неадекватна защита.
Тази ситуация се усложнява от дюза, която е твърде малка за приложението и е по-податлива на по-голямо и по-бързо натрупване на пръски. По-малките дюзи могат да осигурят по-добър достъп до ставите, но също така да възпрепятстват газовия поток поради по-малкото напречно сечение, разрешено за газовия поток. Винаги имайте предвид променливата на изпъкналостта (или вдлъбнатината) на контактния връх към дюзата, тъй като това може да бъде друг фактор, който влияе върху потока на защитния газ и порьозността при избора на дюза.
Имайки това предвид, уверете се, че дюзата е достатъчно голяма за приложението. Обикновено приложения с висок заваръчен ток, използващи по-големи размери на телта, изискват дюза с по-големи размери на отвора.
При полуавтоматични приложения за заваряване периодично проверявайте за пръски от заваряване в дюзата и ги отстранявайте с помощта на клещи за заваряване (заваръчни машини) или сменете дюзата, ако е необходимо. По време на тази проверка се уверете, че контактният накрайник е в добра форма и че газовият дифузьор има чисти газови отвори. Операторите могат също да използват смес против пръски, но трябва да внимават да не потапят дюзата в сместа твърде далеч или за твърде дълго, тъй като прекомерните количества от сместа могат да замърсят защитния газ и да повредят изолацията на дюзата.
При роботизирана заваръчна операция инвестирайте в станция за почистване на дюзи или райбер за борба с натрупването на пръски. Това периферно устройство почиства дюзата и дифузора по време на рутинни паузи в производството, така че да не влияе на времето на цикъла. Станциите за почистване на дюзи са предназначени да работят заедно с пръскачка против пръски, която нанася тънък слой от сместа върху предните компоненти. Твърде много или твърде малко течност против пръски може да доведе до допълнителна порьозност. Добавянето на въздушна струя към процеса на почистване на дюзите също може да помогне за изчистването на свободните пръски от консумативите.
Поддържане на качество и производителност
Като следите процеса на заваряване и познавате причините за порьозността, прилагането на решения е сравнително лесно. Това може да помогне за осигуряване на по-дълго време за включване на дъгата, качествени резултати и повече добри части, преминаващи през производството.
Време на публикуване: 02 февруари 2020 г